3 Simple Techniques For Crossdock Warehouse
Wiki Article
Sacramento Crossdock Warehousing Things To Know Before You Get This
Table of ContentsSacramento Warehouse Things To Know Before You Get ThisFascination About Sacramento Cross DockThe Ultimate Guide To Sacramento CrossdockNot known Details About Sacramento Warehouse The Only Guide to Crossdock Warehouse
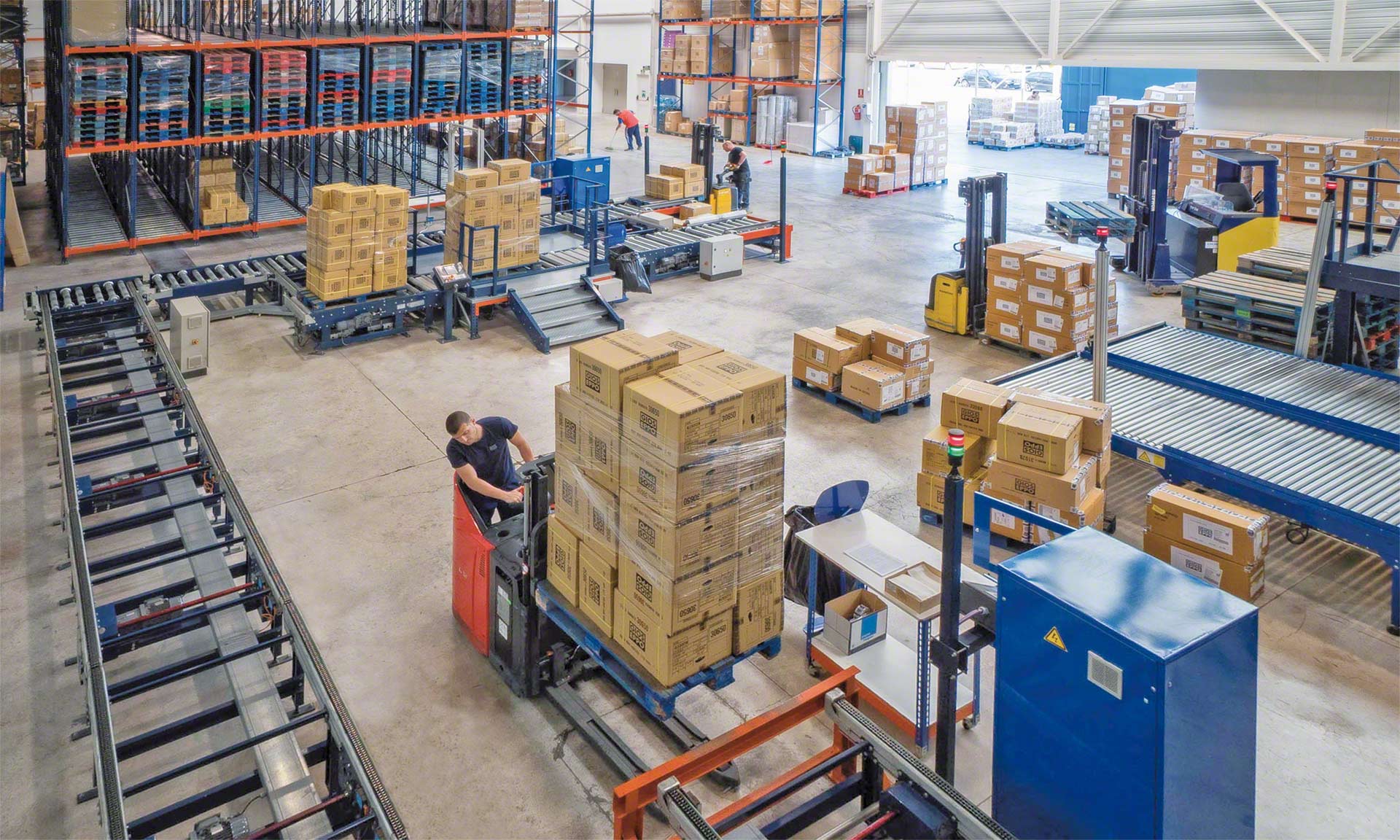
As a part of SCM, reliable supply management might cause a more powerful supply chain. Another reason good warehousing is essential to SCM is that it provides a method for services to guarantee the availability of the right items at the right location whenever the time is. It enhances the utility value of the items in this way - Sacramento Warehouse.
Customers anticipate to recognize when roughly their acquisitions will certainly be supplied after an order is put. The expertise relating to the shipment time boosts their self-confidence. A few of them pay faster because of this. Obviously, they become a lot more hesitant when unpredictability exists around the timely delivery of items. Nowadays, delivery rate seems to be among the significant variables that customers consider when picking a product and also choosing whether to wage the purchase.
10 Simple Techniques For Sacramento Cross Dock
A substantial factor to buy developing a warehouse is the numerous well-known financial benefits that include it. Not just the boosted efficiency of the supply chain but additionally the storage facility's storage space capacity and also exactly how it offers as a main area for your items contribute to its economic advantages.These points can be seen or realised through debt consolidation and also buildup operations. Here's a better check out just how loan consolidation and build-up can assist lower expenses: With debt consolidation procedures, there's no requirement to ship products separately from several sources because they might be provided to your warehouse as stocks. Once an order is placed, you or your team can load and also deliver the item out from there.
Not just that, however good warehousing likewise enhances customer support and offers financial benefits. All of these things could bring about greater profits as well as improved organization profitability.
The Buzz on Crossdock Warehouse
Delivering materials for order satisfaction. People who fill items right into a storehouse and others ("pickers") that fill up orders in a true distribution facility, plus those that manage the center and also operation. Security to safeguard stored items. Access to affordable transport to bring products in or move them out as orders are met.They also require to make sure that products are saved in a risk-free and also protected fashion. Stockroom examples include retailers, circulation centers, freezer facilities, and also manufacturing plants. In stores, items are stored and arranged in a storehouse and shipped to customers or various other shops. Distribution facilities are used to shop and also distribute products to numerous locations.
Warehousing best technique is to utilize RF Scanners, or comparable innovations, to additional enhance stock accuracy and also actual time supply monitoring. Very closely linked with Obtaining, Putaway is the last phase of incoming handling. Putaway is the procedure of literally, as well as methodically, putting items into their appropriate final storage areas (Crossdock Warehouse). Staff selects Product to putaway from Putaway Staging area, Generally Pallets or Carts with Item prepared to be putaway, Utilizing RF Scanner, identify what cart/pallet/job you are doing away with and also check distinct identifier to begin Putaway, Picker travels to location to position product for storage, Perfect finest in class systems tell staff where to position item, but lots of stockrooms still have personnel place item where why not try this out they understand there is empty room (with some standards applied)RF Check Item being putaway as well as Location where the Item is putaway, Continue process (most likely to place and place supply) up until whole order, pallet, cart, and so on is complete Weight and also dimensions of product/pallet being putaway, Stowability of Product (ie breakable, stackable, and so on)Transaction quantity (best-sellers placed close vs NOT far away)Amount received, Worth of product, Choose Kind of Product (single choice, batch choice, cluster choice, zone choice, etc) Accurate Putaway is imperative in the stockroom operation, making certain that Product can be conveniently located specifically when it is needed.
Sacramento Crossdock for Dummies

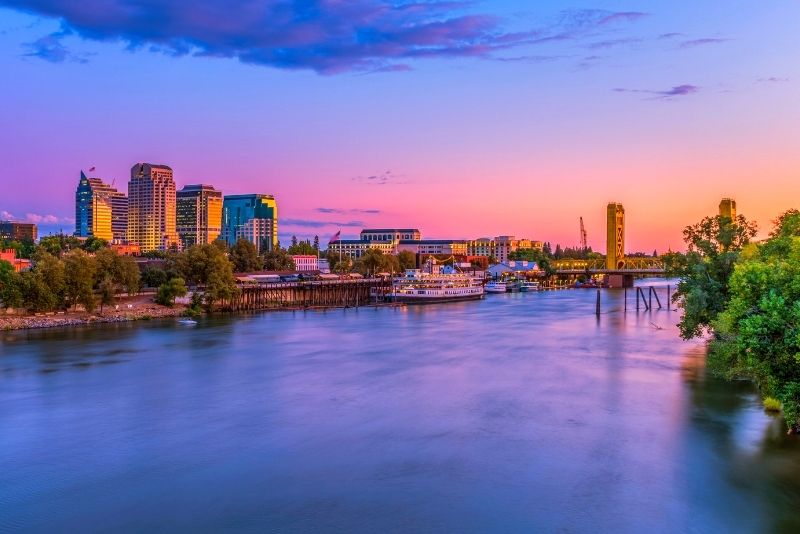
Comparable to just how Getting lays the foundation for a precise supply, Selecting lays the foundation to accurately meet a client's order. Picking is the procedure of gathering Products to satisfy a client's order demand. Picker is assigned Select(s)There are numerous select techniques, each operation is one-of-a-kind in what is most reliable for their needs, Area picking, set picking, solitary order picking, wave selecting, as well as more, Making Use Of click to investigate RF Scanner, or similar, start picking by going into the Unique Choose Identifier (batch #, Order #, SO #, Choose #, various other recommendation)Picker is transmitted through the Select Path (ideally based upon optimization logic) to accomplish the Choose, scanning Products and also Locations as they progress, Chosen things may be put in totes, pallets, carts, shelf, etc throughout pick, Fully chose orders delivered to next stage of process, Picked orders might be delivered to a Quality assurance area, Packing/Shipping area, or straight to outgoing staging (if pick to label procedure) depending upon procedure Limitations/abilities of current Stockroom Management System (WMS)Volume of Orders # of Product Lines per Order, Sort of storage space media (shelving vs racking vs ground pallet storage)What the Packaging and also Shipping Process appears like (carefully intertwined to Selecting)Product need additional focus throughout packaging? Transportation Administration System (TMS) with the ability of giving delivery labels before items are picked? A lot more! Storehouse Format Selecting have to be done accurately, with quality control steps in area post-picking, to achieve customer order fulfillment accuracy near 100%.
If throughout delivering the weight is not within the specified tolerance range, after that the customer will certainly be prompted to take action, Measurement resistance check throughout Delivery, Comparable to Weight webpage resistance based on system measurement data Packing and Shipping is a major emphasis of stockrooms, as it typically comes to be a traffic jam given that Order Processing Time must be as short as possible to fulfill client expectations.
Do NOT sacrifice high quality! It is crucial to note, depending upon the stockroom procedure Packaging may be combined with the Picking process. Inventory Control is an important component of all warehouse procedures. You can assure the supply at the storehouse is exact and also updated with a well defined Supply Control procedure.
Some Known Details About Sacramento Crossdock Warehousing
Cycle Counts and Complete Stock Counts are tools associated with keeping Supply Control. Cycle Counts occur continually while regular procedures continue, but Complete Stock Counts happen periodically and also need all product motion to cease until a complete precise matter is completed. Closure all supply activities, finishing all Item Activities in the Stockroom (physically and methodically)Guarantee all incoming as well as outbound orders that have actually been physically refined, have additionally been processed in WMSBreak storehouse team right into groups to matter (often 1 person team okay)Groups are appointed areas to count Assign small-medium locations to count, then groups check in for even more areas as needed, Groups count assigned locations, recording matters of item per location, Groups typically using RF Scanners to tape-record counts, Otherwise have to do paper-based which is tough to achieve a Blind Matter, Group reports back when completed and get next Matter Project, After locations are Counted, the Manager/Lead evaluates all Differences, Manager designates various Team to recount the distressed Products and/or Locations, If second team counts exact same as first group, make inventory modification to match physical matter.Report this wiki page